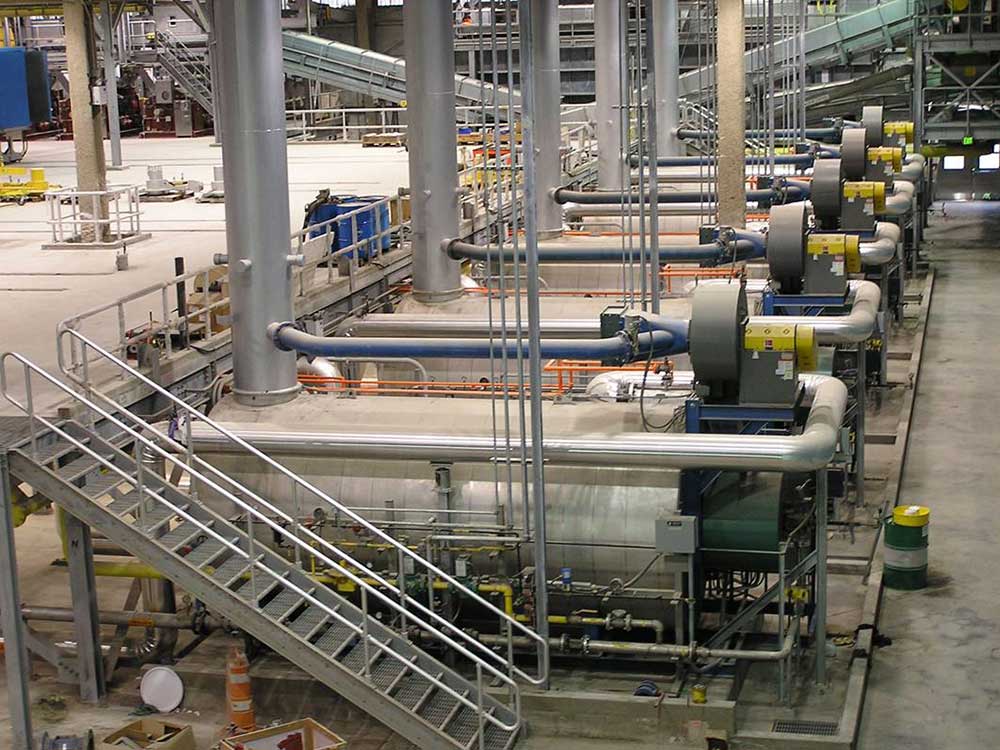
Thermal Fluid Heating Systems
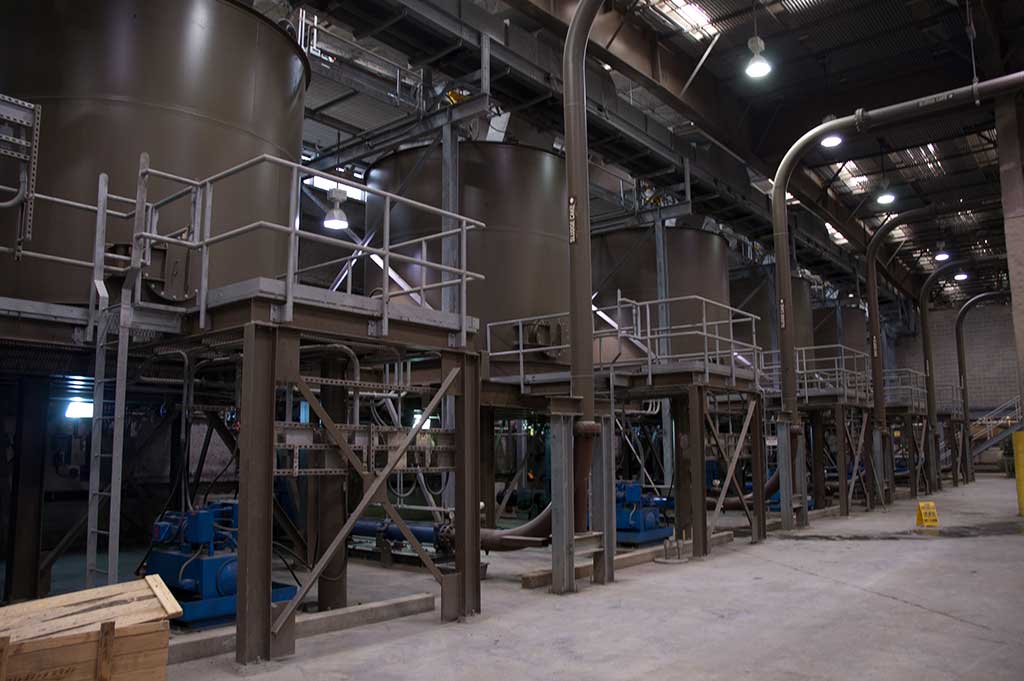
Flat Bottom Sliding Frame Storage silos
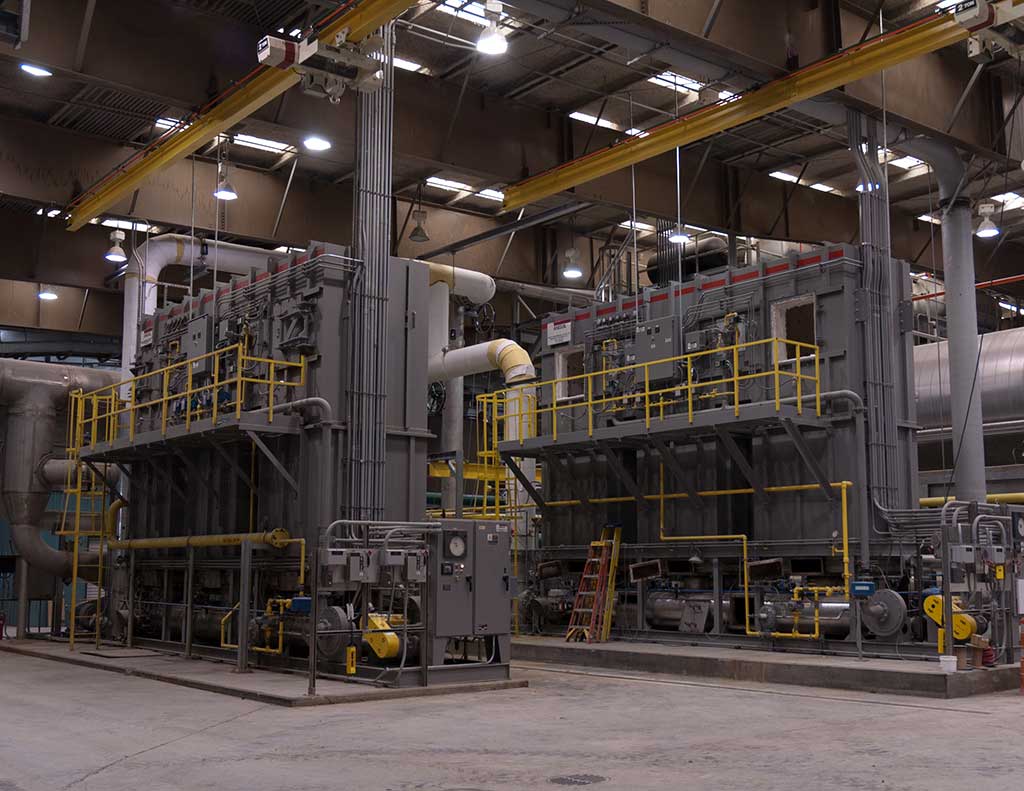
Regenerative Thermal Oxidizers
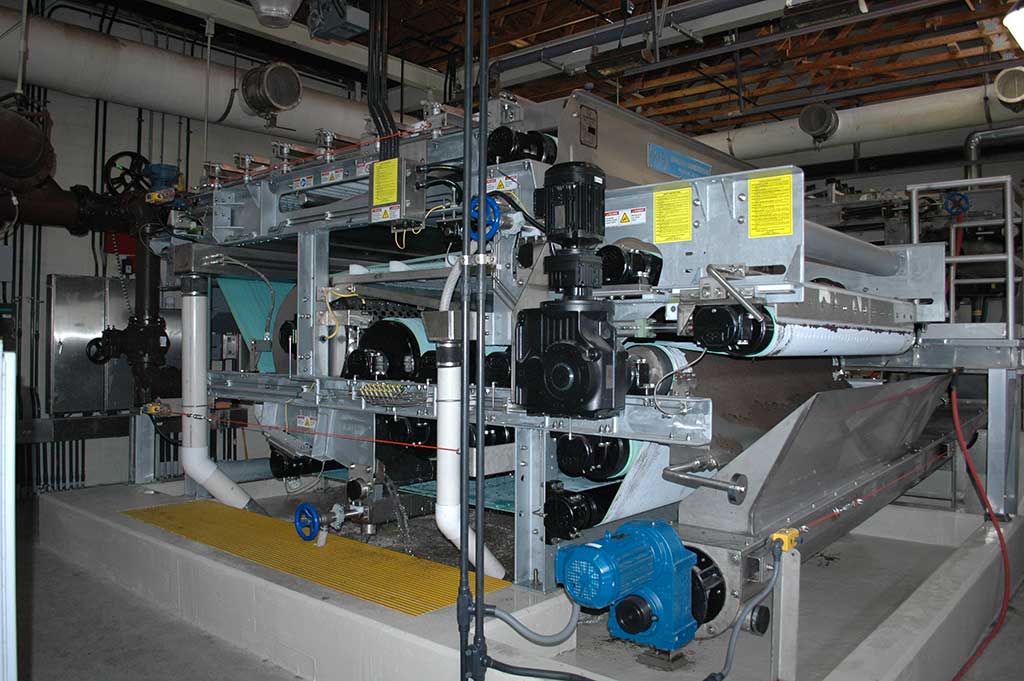
Belt Filter Press for Sludge Dewatering
R3M developed the first US application of thin film sludge drying an existing biosolids alkaline stabilization process for the Middlesex County Utilities Authority, a regional wastewater utility that provided wastewater treatment for over 800,000 people in 36 municipalities.
The project involved the evaluation and design of five (5) Indirect Thin Film Dryer (ITFD) streams that provide capabilities to dry belt press dewatered sludge from 25% DS to approximately 55% DS. The process was designed to fit within an existing product storage building, limiting headroom for maintenance of the dryer systems.
The resulting dried product is introduced into an alkaline stabilization process before it is used as intermediate daily cover at the Middlesex County Landfill. The system was designed to process an average of 157 Dry Tons per day (DTPD) at 27% feed solids when operating three dryers, with a maximum feed of 246 DTPD with one dryer stream off line for regular maintenance.
The each of the five ITFDs are part of an overall drying process that includes flat bottom sliding frame silos, materials handling belt conveyors; five (5) Thermal Fluid Heating Systems including 16 MMBTU TF dual coil heaters with Flue Gas Recovery; vapor and condensate systems including condensers and heat exchangers that utilize plant effluent as a cooling medium; SCADA Control System for monitoring and controlling of all processes integrated with Motor Control Centers using DeviceNet, Ethernet and fiber optic communications systems.
Common process equipment to all dryer streams included Dewatered Sludge cake storage, pumping and conveying systems; Vapor off-gas treatment system including a 5,000 cfm Regenerative Thermal Oxidizer to achieve thermal destruction of VOCs from all five dryers at approximately 1,500° F; and Odor Extraction systems that were integrated with existing odor control processes.
The project also included modifications to the existing MeadowLife alkaline stabilization process, development of an overall SCADA monitoring and control system, modifications and expansion of existing materials handling primarily using belt conveyors, and modifications of existing sludge pumping capabilities from the ten existing belt filter presses.
Our experience in sludge processing and residuals management includes process equipment evaluation with associated chemical feed, odor control, and process control systems provides can be applied to a client’s individual needs.